Test and tag is a safety procedure for verifying that electrical equipment functions correctly and safely in workplace environments. Although some may view it as simply attaching a coloured label to an appliance, the process carries significant weight in safeguarding employee safety, ensuring compliance with laws, and protecting valuable equipment from damage and failure. This article highlights why tests and tags are more than just stickers.
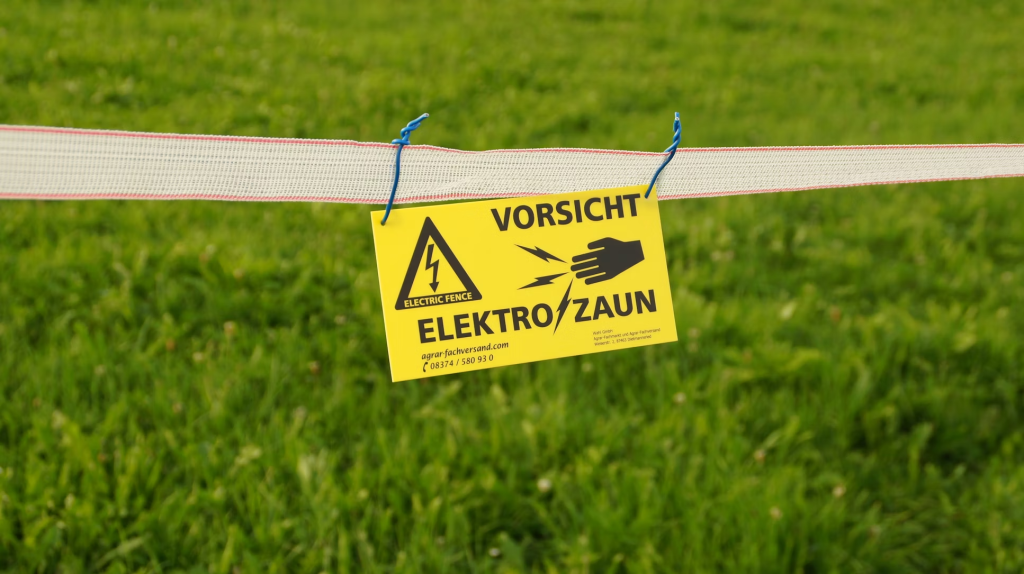
For professional and reliable test and tag services in Melbourne, consider contacting experts in the field.
The Legal And Compliance Obligations Of Test And Tag
Workplace Safety Regulations In Australia
In Australian workplaces, test and tag play a key role in compliance with safety regulations. The Work Health and Safety (WHS) laws require all businesses to ensure that electrical equipment is safe. To achieve this, a competent person must perform routine inspection and testing.
- Occupational Health and Safety Act 2004 sets out the duty of employers to protect workers from electrical hazards.
- AS/NZS 3760:2022 is the current standard that details the procedures for testing and tagging. It specifies the types of tests required, the intervals for testing, and how to record and report the results.
Employers must document all tests and keep a register of equipment and test outcomes. This documentation is critical in case regulatory authorities inspect the facility. Not conducting proper testing places workers at risk and can lead to legal consequences. These may include penalties, potential lawsuits, and reputational damage to the business.
Preventing Workplace Accidents
Electrical accidents are often sudden and severe. They may lead to injuries such as burns, electric shock, and even fatalities. Fires caused by electrical faults can damage infrastructure and disrupt business operations for extended periods.
Test and tag procedures aim to prevent such incidents by identifying and removing faulty or damaged equipment from service before harm occurs. The process involves thorough inspection and electrical testing to detect:
- Exposed wires
- Damaged plugs or leads
- Loose connections
- Moisture or contamination within devices
Early detection allows businesses to act immediately and replace or repair the equipment. This proactive measure prevents accidents and contributes to a safer work environment. By implementing a regular test and tag schedule, employers send a clear message: safety comes first.
Test And Tag: More Than Just A Sticker
Enhancing Workplace Safety
Many people mistakenly believe the test and tag sticker is the entire process. The tag is merely a visible confirmation that the equipment has passed inspection. The real value lies in the testing process carried out before tagging.
When a certified technician carries out the testing, they assess the appliance’s physical condition and perform specific electrical tests such as:
- Earth Continuity Test – Ensures the earth wire is connected properly.
- Insulation Resistance Test – Detects any leakage of electricity from wires.
- Polarity Test – Verifies that the active and neutral wires are correctly aligned.
These tests ensure the equipment does not pose an electrical hazard to users. A sticker alone cannot achieve this. Rigorous inspection and testing reduce risk.
The presence of tags can also serve as a deterrent. When staff see test tags regularly updated, they are more likely to report concerns about appliances that show signs of wear.
Regular Testing Promotes Equipment Longevity
One of the less-discussed benefits of test and tag is that it helps extend the life of your electrical assets. Regular inspections allow businesses to monitor equipment performance and catch problems early.
Let’s consider the benefits more closely:
- Reduces Equipment Downtime: Regular checks mean issues are caught early, reducing breakdowns and operational disruptions.
- Saves on Replacement Costs: Companies can avoid unnecessary equipment replacement by identifying repairable faults early.
- Improves Asset Management: Businesses gain insight into how equipment performs over time. This helps plan future investments or upgrades more effectively.
Maintaining equipment through a scheduled test and tag program supports business continuity. Avoiding equipment failure is critical in industries where reliability is vital, such as construction, healthcare, and manufacturing.
Helping Businesses Avoid Legal Trouble
Non-compliance with test and tag requirements doesn’t just risk fines—it can destroy a company’s reputation. In workplaces where safety is overlooked, the aftermath of a serious incident could result in prosecution. Insurance providers often request proof that workplace equipment is being properly maintained.
An insurance claim following an accident or fire may be denied without evidence of routine testing. Test and tag offers a documented audit trail. These records show that the business took all reasonable steps to ensure safety in case something goes wrong.
This documentation can significantly reduce the employer’s liability. It’s also worth noting that businesses without a test and tag program may not obtain specific contracts, especially on construction or government sites where compliance is non-negotiable.
Why Test And Tag Is Critical For Your Business
Risk Management
Any business that uses electrical equipment needs a strategy for managing its associated risks. Relying on visual inspections alone isn’t enough, as electrical faults are often invisible to the naked eye.
Introducing a structured test and tag procedure ensures that:
- Every piece of portable equipment is checked at consistent intervals
- Faults are detected early, before becoming hazards
- Up-to-date data support maintenance schedules
This process builds a strong safety culture within the business and shows that management is committed to the well-being of its staff and clients.
Cost-Effectiveness
From a financial perspective, the test and tag process is highly efficient. Compared to the potential losses caused by faulty equipment, the cost of regular testing is minimal.
Let’s compare:
- The cost of test and tag – Relatively low per device, especially as part of a routine visit.
- The cost of an electrical accident – Includes medical bills, legal fees, damaged property, downtime, and lost productivity.
Regular testing reduces emergency call-outs, which are more expensive than scheduled maintenance. In sectors where business operations are continuous, such as factories or data centres, avoiding downtime through preventative measures can result in substantial savings.
Insurance And Liability Protection
Workplaces that ignore tests and tags put themselves at risk of insurance issues. Most policies contain conditions requiring businesses to take “reasonable care” to prevent losses. Not testing your electrical appliances could be seen as negligence.
Test and tag also provides:
- Documented proof of safety management: Records from the test and tag provider are valuable evidence in the event of a claim.
- Assistance with audits: Regular testing can help with workplace audits or site inspections by authorities.
- Improved coverage: Some insurers may offer better terms to businesses that demonstrate active risk management practices.
Maintaining updated records from a certified technician also helps with onboarding new staff or expanding operations, as it shows consistent attention to safety procedures.
Conclusion
Test and tag is a foundational part of workplace safety, far beyond the visible sticker on an appliance. It’s a process of inspection, assessment, and documentation that protects people, equipment, and business operations. With benefits ranging from legal compliance to cost savings, test and tag are essential to modern risk management strategies.
While the label may be the most visible part of the process, it represents a series of safety checks and procedures that play a vital role in preventing accidents. By implementing a robust test and tag schedule, businesses affirm their commitment to safety, compliance, and the longevity of their assets. In short, test and tag is more than just a sticker—it’s a business necessity.
Frequently Asked Questions
How Often Should I Test And Tag My Equipment?
The frequency depends on the type of equipment used and the environment in which it is used. For high-risk settings like construction sites, testing may be required every 3 months. In lower-risk areas such as offices, intervals can range from 12 to 24 months.
Who Is Qualified To Perform Test And Tag Procedures?
Only a competent person, usually someone who has completed a nationally recognised test and tag course, can conduct these tests. They must understand the standards involved and be able to use the necessary testing instruments correctly. Certification and experience are key indicators of a qualified technician.
Is Test And Tag Mandatory For All Businesses?
Yes, in Australia, businesses are legally required under WHS laws to ensure the electrical safety of appliances. Test and tag is a recognised method of compliance. It demonstrates a proactive approach to safety and helps avoid legal or insurance issues in case of an incident.